This article describes the critical aspects of processing used for the tubing and metal section bars that form the frame and exhausts of the cars produced for automobile racing. As is known, these cars are actual concentrates of technology. For this reason, these special processes require absolute precision.
The frame of the race car must be lightweight, above all, as the vehicle must be fast. But it must also be very sturdy, because during the race the car will have to withstand severe stresses. In addition, it has to ensure easy handling by the driver.
Winning an auto race can be a matter of a few milliseconds. Often, if not always, two factors are decisive for the outcome of the race:
- The skill of the driver
- The performance of his car
The processing of the pipes that are used to make the car, which is an element of the second group, obviously, is the specific subject of this article.
When we talk about metal pipe processing we have to consider, first of all, the problem of the choice of the metal alloy. The choice of an alloy of steel, aluminum or titanium will depend essentially on two aspects:
- The processes to be carried out on the tubing (they will determine its function)
- The stresses to which the metal tubing will be subject in performing that specific function. Maintenance of the integrity of the alloy is thus another element of primary importance.
The main processes that concern us are bending, cutting and assembly of the tubes making up the frame and exhausts. The absolute precision of the bending angle and of the processes performed with laser tubes are essential requisites for the correct assembly of the car and directly affect its performance in the race.
In the last two years, Tecnocurve has developed special processes for bending steel, titanium and aluminum tubes for the construction of the frame, the exhausts and other parts of the RACE UP TEAM formula SAE.
Birth of a frame: bending and laser cutting of 21 steel tubing
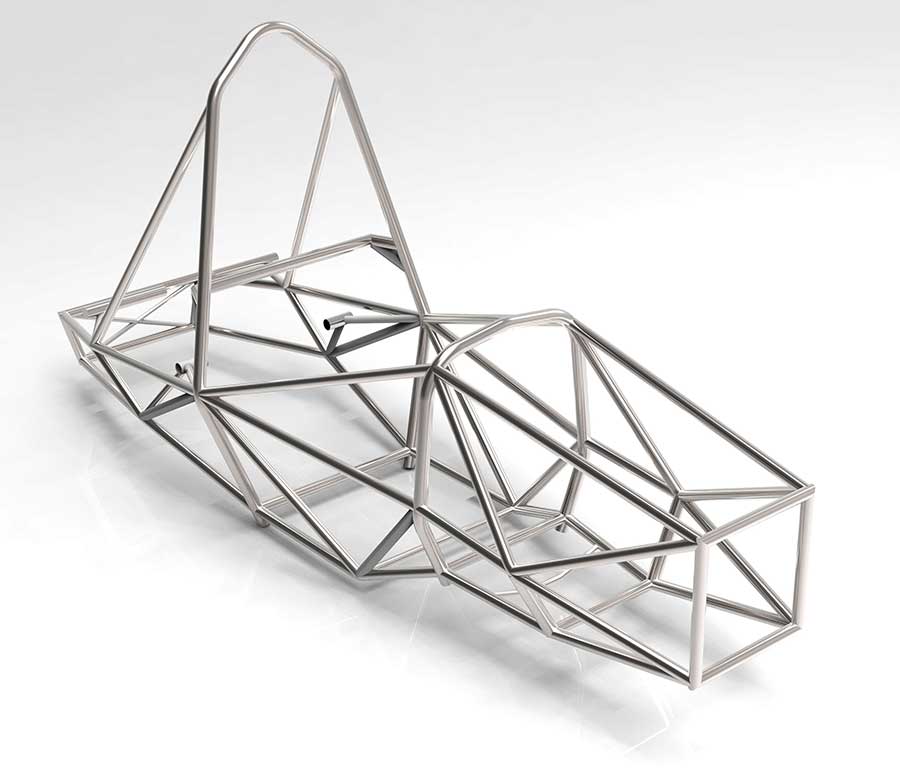
The frame produced for the RACE UP car consists, in total, of 21 special steel tubes. This particular steel alloy makes it possible to produce tubes without welding on the inside, which ensures greater strength and flexibility of the frame, so that it is able to absorb the many stresses to which it is subject during the race in the best possible way.
The tubing is cut and bent with a tube matrix of Ø25×1.5, average radius 90 mm, on CNC equipment, then assembled.
To obtain the maximum precision and accelerate the production process, we used the technique of preliminary perforation with a laser tube before bending the tubing.
Learn more about the advantages of laser perforation prior to bending the tubing.
Welding the frame tubes
Titanium exhaust pipes to improve resistance to vibrations
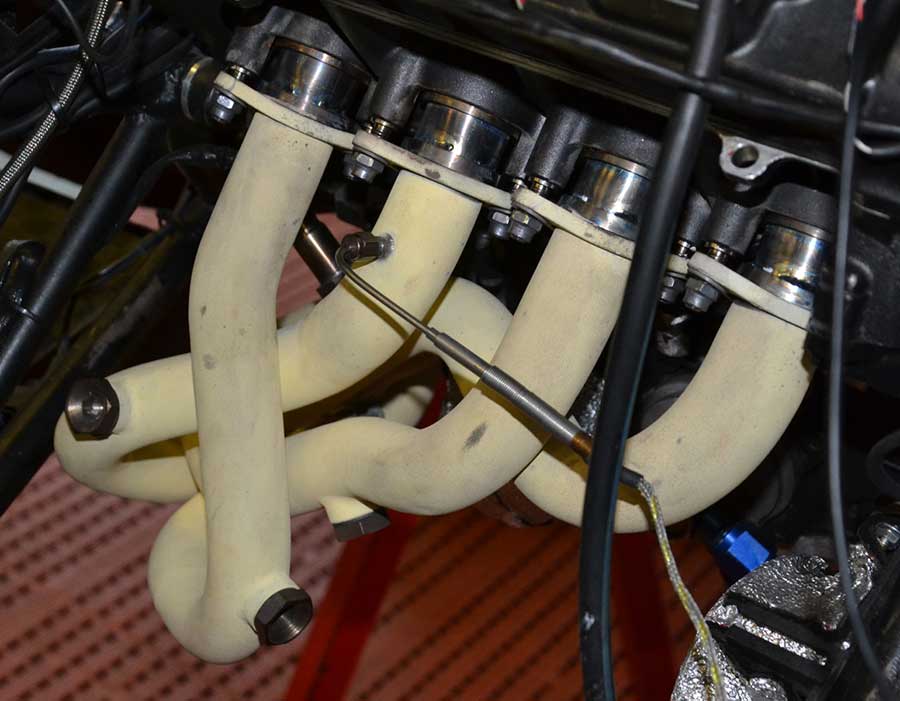
Bending of titanium pipes
The bend radius required for the four exhaust pipes was very narrow (average radius 65 mm) with respect to the cross-section of the pipe to bend (Ø35×1). The bending is done on a pipe-bender that can process pipes from 20 to 40 mm in diameter.
Thanks to special 3D software, we designed and produced a set of special tools in our workshop for bending the exhaust pipes.
The quality of this process is another fundamental element for the successful outcome of the car: the discharge of exhaust fumes has a direct influence on the overall performance in a race.
Aluminum manifolds and couplings
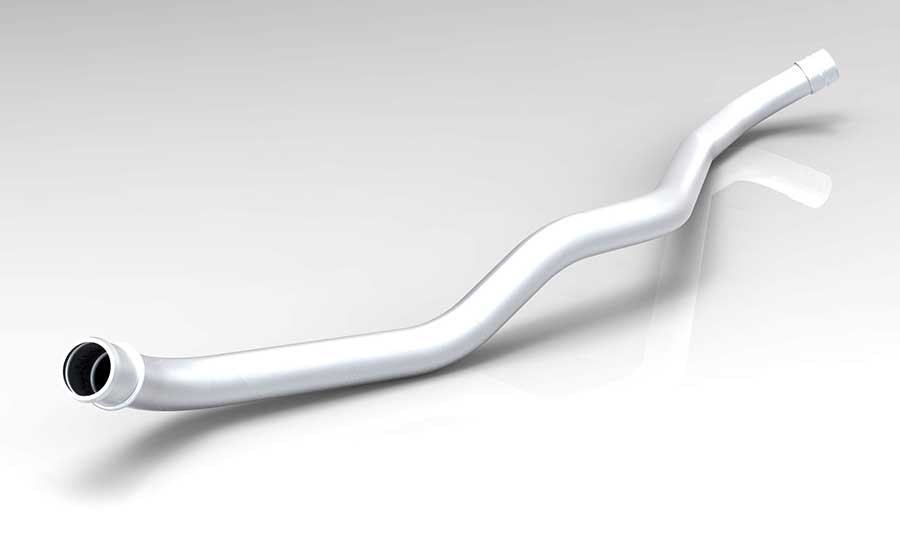
When it comes to parts like manifolds and couplings, however, we prefer to use aluminum. These parts provide the connection between the various “organs” of a car, allowing passage of air, fuel or exhaust fumes.
On these bent pipes we had to produce tapering (or markings). This process, which can be done either by laser or mechanically, serves to engrave the curved pipes with a series of characters specified by the customer (usually indicating the model, supplier and production date) necessary to identify them. This is particularly useful in case of malfunctions.
Formula sae and race up team
The Race Up Team is a group of about fifty students whose annual project is to produce a Formula SAE racing car. Formula SAE is the Formula One of students born in the U.S., now popular worldwide.
Since 2016 Tecnocurve is an official sponsor of the Race Up Team of the University of Padua. We supply them with the bent tubing in steel and titanium for the frame and exhausts of the car.
A challenge that is also one of organization
LEARN more about SAE, THE FORMULA ONE OF STUDENTS
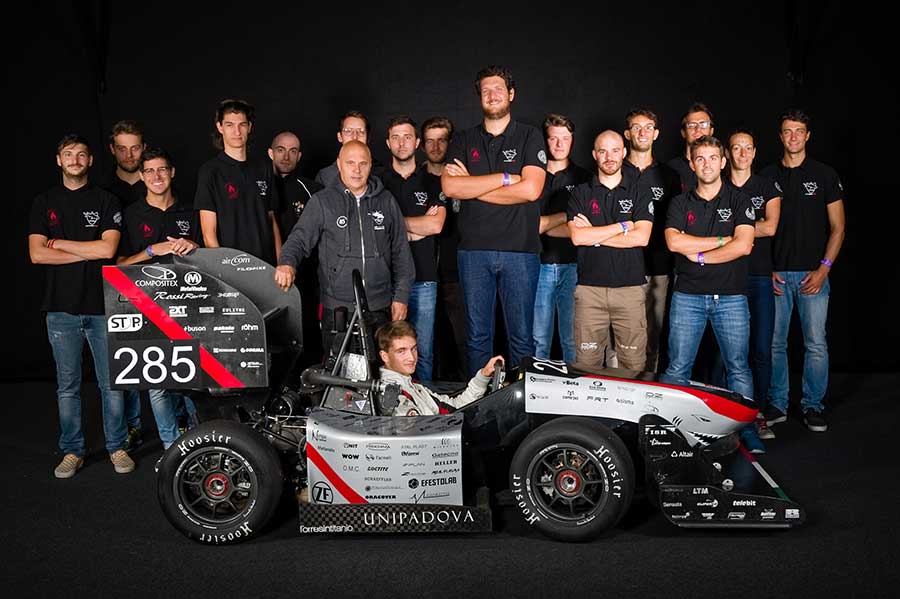
The experience we have acquired from this cooperation has been very useful to us in understanding even better the automotive sector, in the highly specialized area dealing with race cars. We also take particular pleasure in working with such highly motivated kids. They give up their free time to devote themselves entirely to a project that will not bring them any scholastic benefit, but that will help them to succeed in the best possible ways in the business world.
2018 is just around the corner and Tecnocurve has renewed its agreement to cooperate with the Race Up Team. The goal, obviously, is to improve the performance of the Padua team and at the same time increase our experience and skill in internal processing for bent tubing.