This article talks about the techniques for bending and rolling a steel or stainless steel tube.
Steel is one of the most frequently used metals in the production and processing of tubes, tubular parts and structural sections.
Bent steel tubes and pipes are used to manufacture many different products. Examples of these include:
- Garden machinery
- Vehicle cabs
- Rain shelters
- Canopies
- Handrails on stairs
- Ceiling lights
- Streetlights
- Tractors
- Structures used when designing open spaces – benches and cycle racks, for example
- Exercise machines
- Handles, door handles and bar handles
In this article, we look at the key differences between a steel tube and a stainless steel tube. To be precise, we’ll be examining their properties, their application scenarios, and the standards and processing methods – with a focus on tube bending and tube rolling.
Technical properties of steel tubes and pipes
The following table lists the most important properties when determining the quality of a steel tube or a stainless steel tube or pipe:
- elongation
- yield strength
- tensile strength
- rigidity
- hardness
- visual appeal
- weight
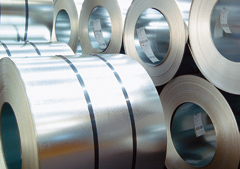
How is a steel tube manufactured?
The commonest manufacturing process used for steel and stainless steel tubes uses coils. Coils are rolls of steel cut from a slab that has been manufactured from cast steel. During the first phase of steel tube production, the coils are cut lengthways to form wide skelps matching the diameter of the steel tube that needs to be manufactured.
These skelps then pass through a series of rolls. The final step is to weld the tube together along its long edge.
This process can be used to manufacture round, square or rectangular tube sections. With the help of matrices, various types of steel sections can be manufactured from a wide range of basic geometric shapes.
Types of steel tubes according to EU standards – alloys
Steel tubes, also called carbon steel tubes (AHS steels), are grouped into two main categories:
- Mild steel: these include highly malleable and easy to work steel tubes with increased mechanical tensile and yield strength, as well as excellent impact strength
- High-carbon steel: while these steel tubes have excellent hardness properties, they are also more brittle. High-carbon steel tubes are harder to process than mild steel tubes. They are ideal for heat treatments such as nitriding or quenching, however.
Each type of steel is given an identifier that specifies its properties.
The following table explains the meaning of these steel codes:
Usage: first letter of the identifying code, namely S, E or P | S | Structural steels | |
E | Engineering steels | ||
P | Steel for pressure vessels | ||
Yield strength: numerical value | 235 | Minimum yield point Rp=235 N/mm2 | |
355 | Minimum yield point Rp=355 N/mm2 | ||
Impact code: two letters | J | Testing strength > 27 J | R (at 20 °C) |
K | Testing strength > 40 J | 0 (at 0°C) | |
I | Testing strength > 60 J | from 2 (at −20 °C) to 6 (at −60 °C) | |
Delivery condition: letter N, M, Q or code G1, G2, G3 | N | Normalised | |
M | Thermomechanically treated | ||
Q | Quenched and tempered | ||
G1; G2; G3 | Rimming steel, rimming steel not permitted, normalised rolled | ||
Usage: letter L, S or W | L | Low-temperature applications | |
S | Shipbuilding | ||
W | Resistant to atmospheric weathering |
If we consult the above table, we can decipher the steel code S275JR as meaning the following:
- S = structural steel
- 275 = minimum yield point 275 N/mm2
- JR = minimum impact strength at 20°
Wikipedia provides a detailed classification of steel grades according to the steel’s carbon content. In this article, we can merely state that the properties of the steel tube, such as ductility, rigidity and its general ease of processing all depend on the formulation of its alloy.
The properties of the steel tube also determine its suitability for a certain use or purpose, such as the production of tools or the construction of buildings, for example.
It’s important to note that, until 2006, almost every country 17used a different code to describe steel alloys. Only in 2006 was a standard introduced that set out a generally applicable set of specifications for steel alloys.
The current code used for our steel above, for example – S275JR – did not exist before 2006, with different codes being used in Germany, Italy, Spain and the United States.
- Italy: Fe 430 B
- Germany: St 44-2
- Spain: AE 275B
- United States: A 529
As you can see from the above example, the steel S355JR was referred to in Italy as FE 510 B, in Germany as St 44-2, in Spain as AE355B and in the US as A633.
Describing steel using the alphanumeric and numerical system
At this point, it should be noted that we’ve previously been using steel codes from the alphanumeric EU (EN) standards. However, there are also some numerical EN standards, as is shown by the following table.
The alphanumeric system describes the steels according to their usage, and their mechanical and physical properties. The numerical system, in contrast, defines the steel using a five-digit code number, where each digit has a separate meaning.
- The first digit designates the material
- The second and third digits specify the material group according to the relevant regulation
- The fourth and fifth digits make up the sequential number for each type of material
EN 10027/1 DESIGNATION (alphanumeric) | EN 10027/2 DESIGNATION (numeric) |
---|---|
S235JR | 1.0038 |
S235JO | 1.0114 |
S235J2 | 1.0117 |
S275JR | 1.0117 |
S275JO | 1.0143 |
S275J2 | 1.0145 |
S355JR | 1.0045 |
S355JO | 1.0553 |
S355J2 | 1.0577 |
S355K2 | 1.0596 |
SJ450JO | 1.0590 |
E295 | 1.0050 |
E355 | 1.0060 |
E360 | 1.0070 |
Tubes made from stainless steel
Tubes made from stainless steel are rustproof, since stainless steel contains a (minimum) percentage of 10.5% chromium, which has the effect of making the steel tube corrosion-resistant.
Stainless steel includes the following types:
- Martensitic stainless steels
- Austenitic stainless steels
- Ferritic stainless steels
- Austeno-ferritic stainless steels
Technical properties of a stainless steel tube
The stainless steels typically used for tubes that will be bent are austentic steels, particularly:
- AISI 304
- AISI 316
What does AISI stand for?
The acronym AISI stands for American Iron and Steel Institute, which is the body that was responsible for creating the standard behind the AISI definitions.
STAINLESS STEELS |
---|
AISI 301 |
AISI 304 |
AISI 304L |
AISI 310 |
AISI 310S |
AISI 316 |
AISI 316L |
AISI 321 |
AISI 410 |
AISI 420 |
AISI 430 |
The acronym AISI is the standard designation for stainless steel and is followed by three digits. The following table explains the meaning of the first digit:
AISI 2XX | Austenitic chromium-nickel-manganese stainless steel |
AISI 3XX | Austenitic chromium-nickel stainless steel |
AISI 4XX | Ferritic or martensitic chromium stainless steel |
AISI 5X | Martensitic stainless steel with chromium steel |
AISI 6XX | Precipitation hardening chromium stainless steel |
The last two digits, which are not specified in the above table, are used to distinguish between the various types of material.
The AISI acronym can also be used together with a letter, which has the following meanings:
L | Presence of carbon at a very low percentage |
Ti | Presence of titanium |
F | Presence of sulphur |
N | Presence of nitrogen |
Difference between a steel tube and a stainless steel tube
Metal alloy | Composition |
Steel | Mostly iron and carbon |
Stainless steel | Mostly carbon, chromium and nickel |
Steel tube | Stainless steel tube | |
---|---|---|
Market price | – Expensive | + Expensive |
Weight | Same | Same |
Surface quality | Matt | Glossy, reflective |
Corrosion-resistant | No | Yes |
Welding | + Easy | + Difficult |
Typical usage | Concealed tubes, unless these have been given a special finish (e.g. coated or galvanised) | Normally visible tubes without the need to give the tubes special treatment |
Often, a stainless steel tube is considered to be ‘better’ on account of its corrosion resistance and mechanical properties. In reality, however, the metal alloy used for the tube – steel or stainless steel – should be chosen based on the following three factors:
- Price
- Weight
- Final use or intended purpose
When is a stainless steel tube the better choice?
A stainless steel tube does not corrode (is rustproof): for this reason, it’s often used for outdoor applications, especially in places exposed to strong bases (such as in coastal areas) or strong acids.
Normally, a stainless steel tube is often preferred to a steel tube in cases where the appearance of the tube surface is important, because the tube will be permanently visible.
The following is a list of industry sectors in which tubes made from stainless steel are typically utilised:
- Food industry
- Shipbuilding
- Interior design – chairs, coat hooks
- Urban structures
- Plant systems
- Swimming baths
- Medical sector
- Exercise machines
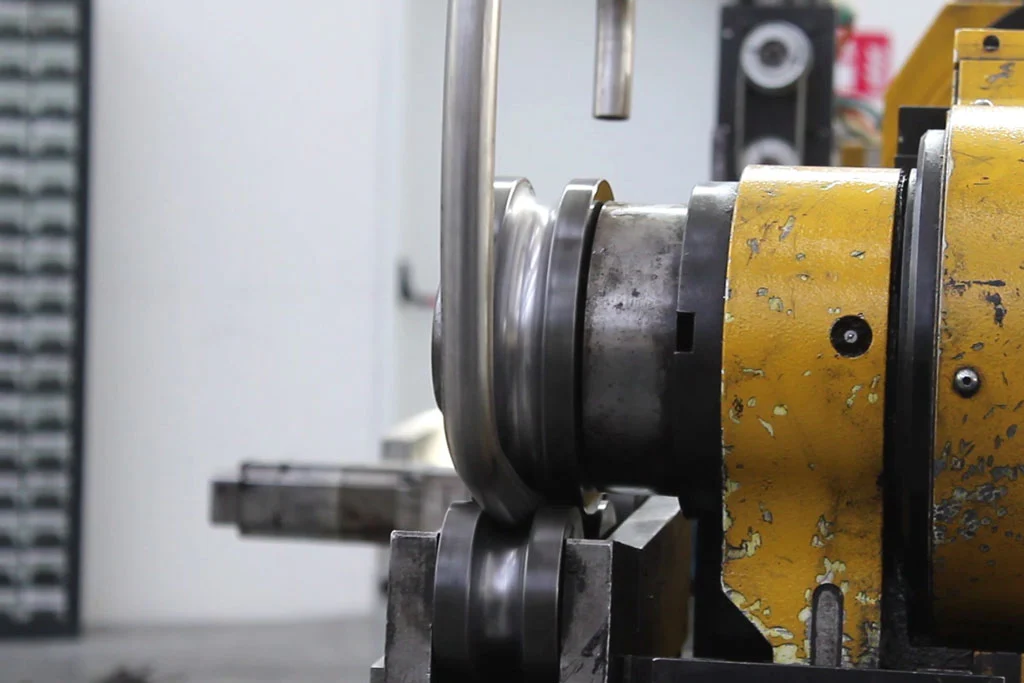
In this video, we can see how a tube made from stainless steel with a 20×2 diameter is being bent to create a bar handle for the seats in a merry-go-round to be installed in an amusement park.
The processing here is tube rolling (roll bending): the tube is given 4 bends with a fixed bending radius and 3 bends with a variable bend radius. The machine used for processing is a CNC tube bending machine, which enables two different devices to be used at the same time.
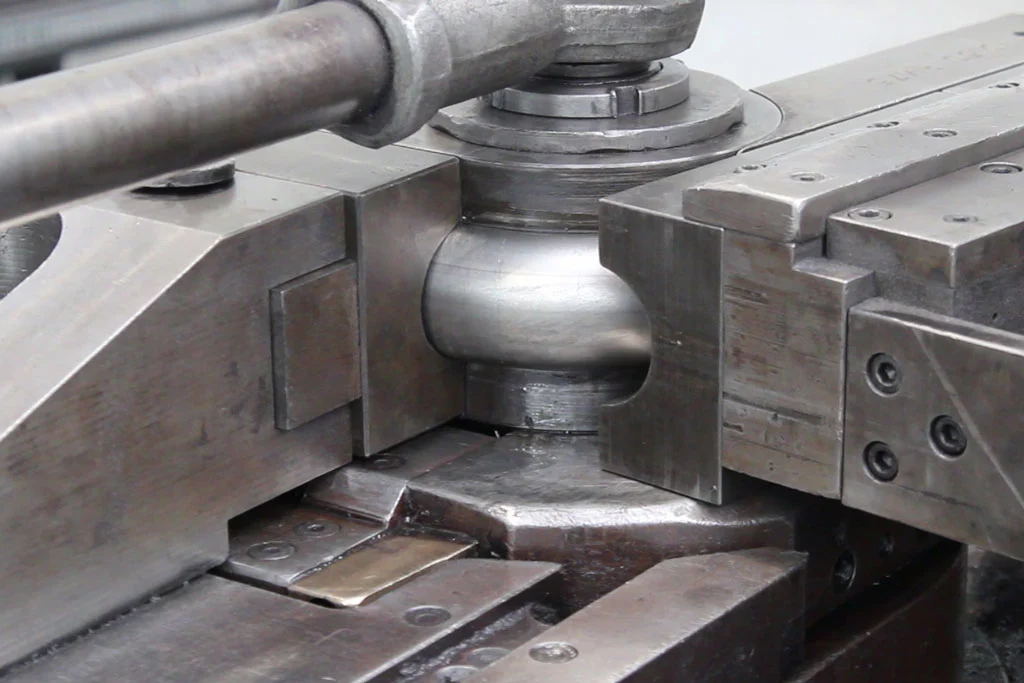
In this video, we see a different set of steps being applied to process a stainless steel tube. This tube will be used to manufacture an advanced beer tapping system. After the first cutting stage, the stainless steel tube is lathed at one end. The tube is then bent before being moved to a machine centre, where it receives a threaded hole. This cannot be done before cold bending, since the hole to be drilled is too close to the bent part of the tube.
When is a steel tube the better choice?
The steel tube – or carbon steel tube – is preferable to a stainless steel tube if it needs to be welded. Another reason why steel tubes are often chosen instead of stainless steel tubes is their much lower price.
Last but not least, steel tubes also offer a larger selection of finishing options that can be carried out as part of processing. Steel tubes are also generally more robust. Steel tubes are typically used in the following industry sectors:
- Lightweight construction
- Medium-heavy/heavy engineering
- Manufacture of agricultural machinery
- Manufacture of cabs for tractors and other machines
- Construction of various metal structures
- Manufacture of industrial sweeping machines
- General fittings
- Machinery for forest management
- Funiculars
- Railway fittings, especially in window frames (also using aluminium), armrests for seats as well as handles
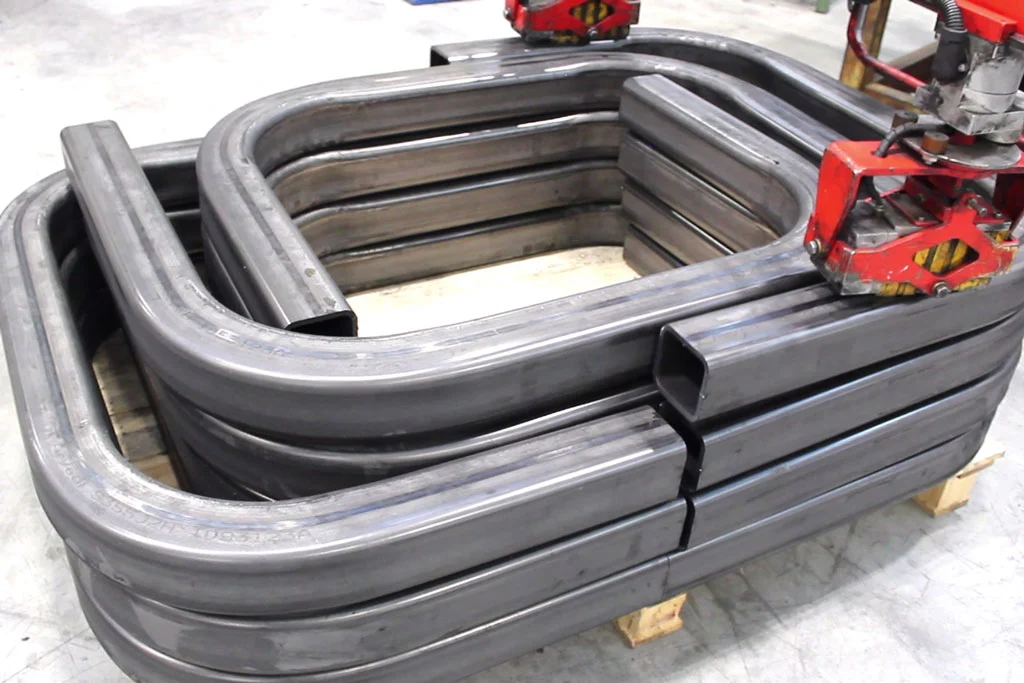
This video shows the bending of S355 steel tubes with a 100x100x8 cross-section. These steel tubes will be used in the production of machinery for the agricultural sector.
Steel tube bending: methods and processes
Together with welding and laser cutting, pipe bending and pipe rolling are the two most important steps used when processing a steel tube.
Steel tubes are bent using specialised machines called tube bending machines.
With this method of tube processing, the tube is bent – using cold or hot deformation – over a fixed radius, which is also termed the bending radius.
Roll bending for steel tubes utilises parts called tube rolls. The tube is bent by passing through 3 or 5 of these rolls. Rolling a steel tube differs from simple bending, because rolling allows the choice of specific bending radiuses for the tube.
The bending radius that can be achieved for a steel tube with the application of tube rolling is also much larger than the radius achievable simply by cold-deformation bending.
The clip below illustrates a series of bent tubes, tubular parts and special-purpose sections made from steel, stainless steel and aluminium, which were bent using our high-precision CNC tube bending machines.
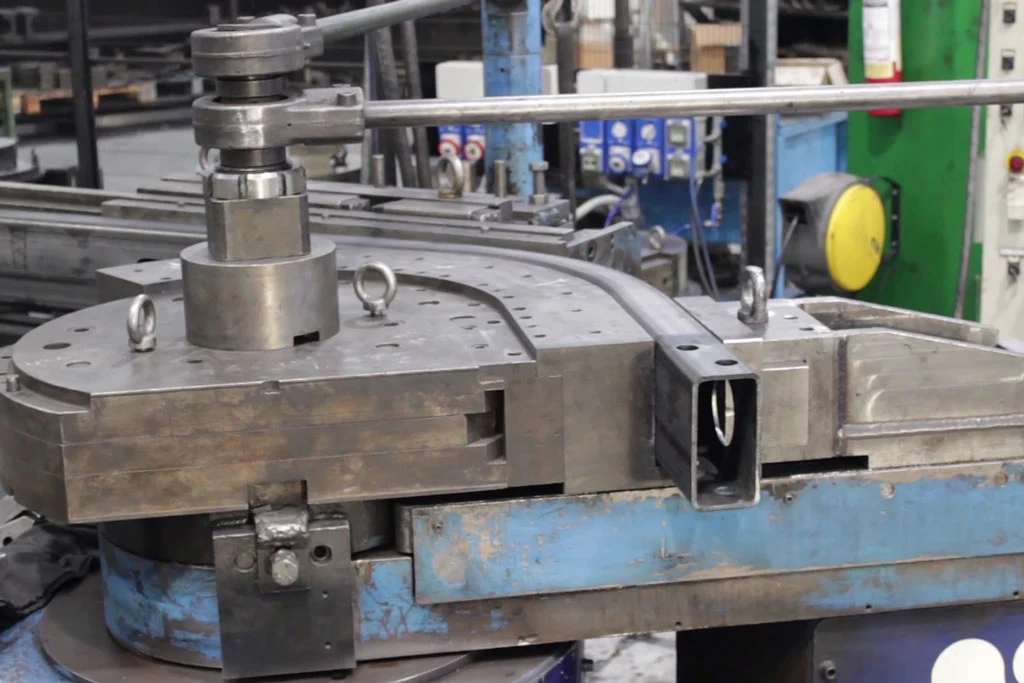
Other processing options for steel tubes
- Laser cutting – This machine not only cuts long tubes into shorter ones but can also drill and countersink holes, make mitred cuts, create eyelets and inscribe lettering. In fact, the laser cutting machine is now an integral part of tube processing work, quite apart from its primary task of making high-precision cuts on steel tubes.
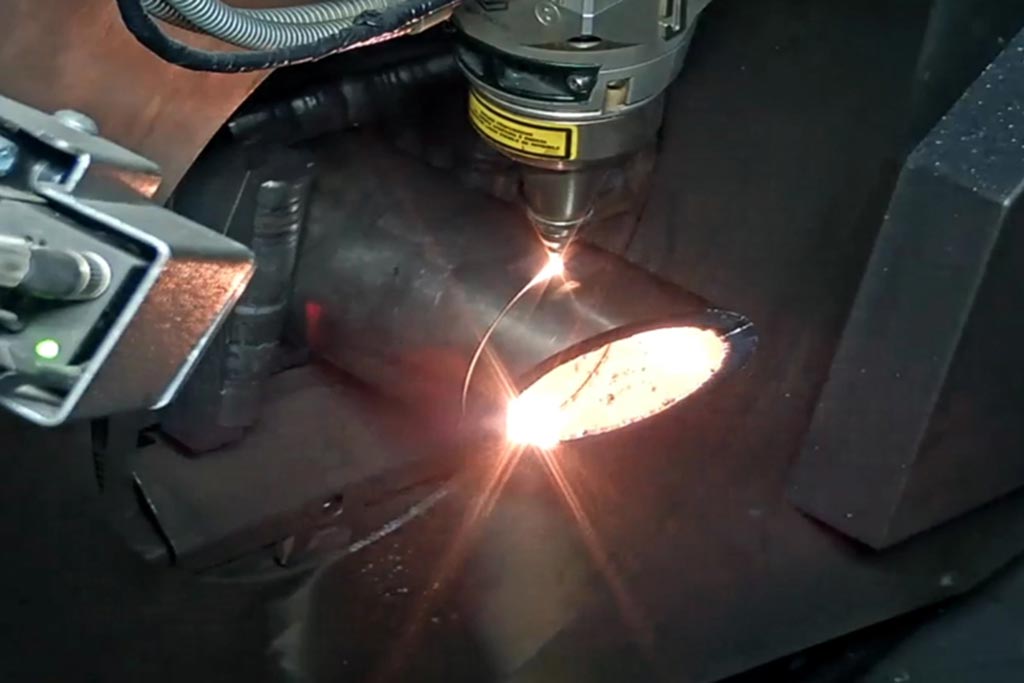
- Welding – Tube welding is a process used to join various kinds of tubes and pipes together. The final intended use of a bent tube made from steel almost always requires the tube to be joined to other tubes or plates in order to obtain the final product.
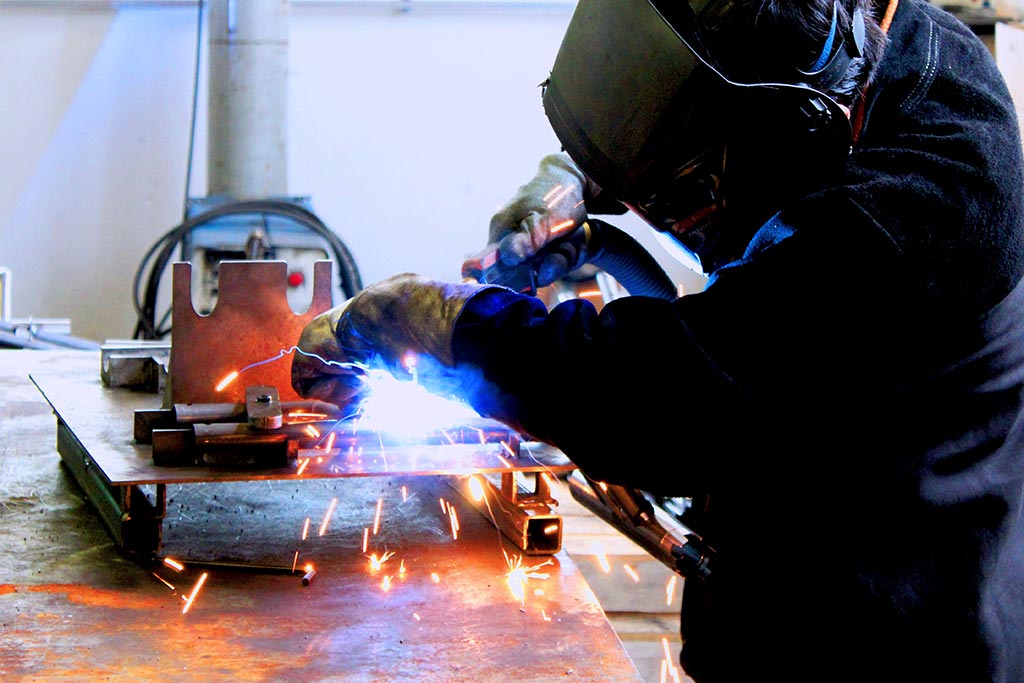
- Milling – Milling uses special-purpose equipment called ‘machining centres’ to perform a wide range of processing tasks on the steel tube, especially drilling and cutting. Machining centre processing work often involves tasks that cannot be completed until the tube has actually been bent.
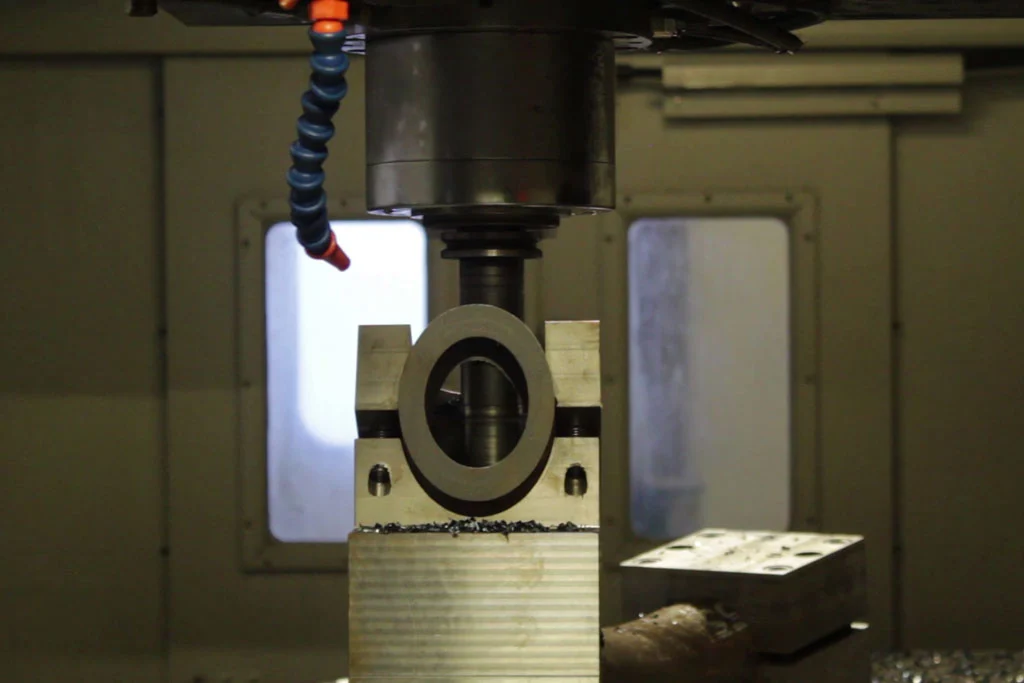
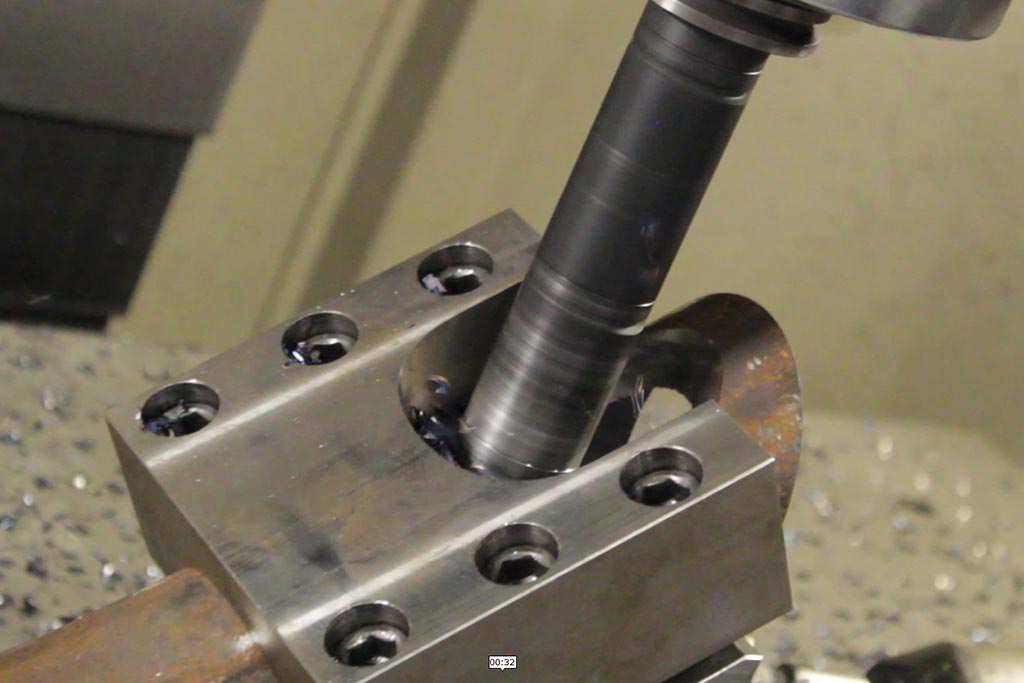
- Lathing – A processing step used to reduce the thickness of the steel tube.
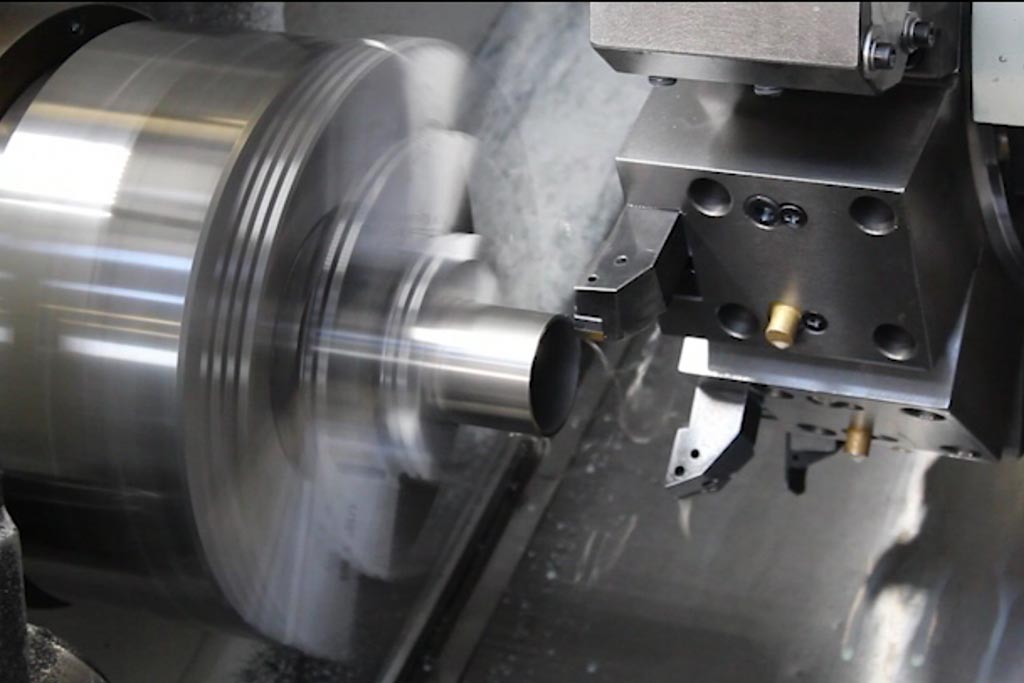
- Flattening – This is an end-forming technique used on the tube ends.
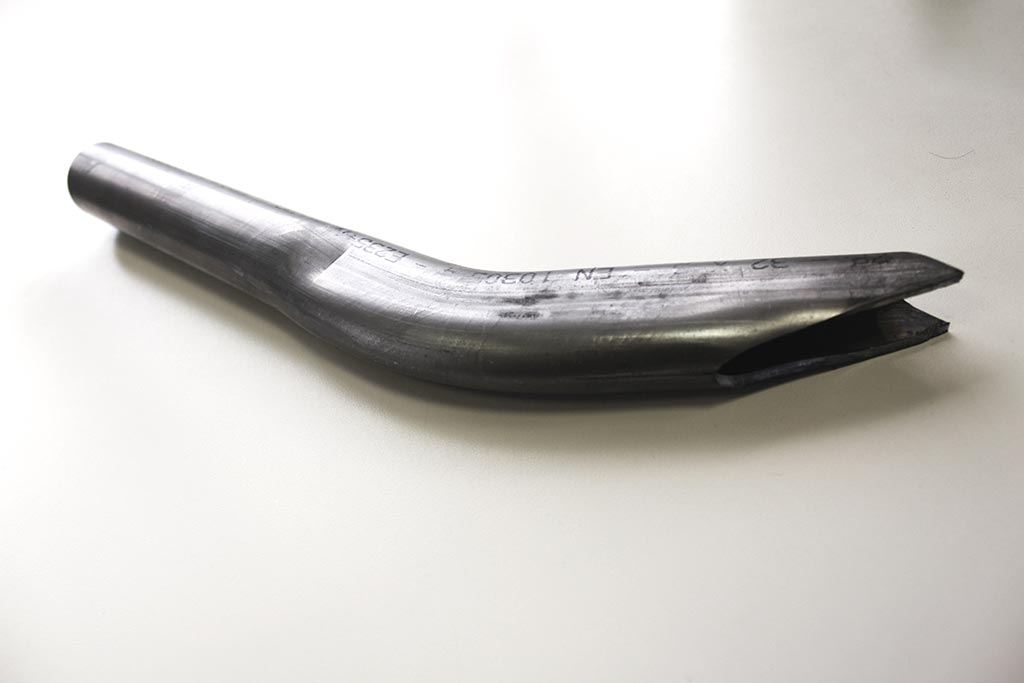
- Mechanical marking – This lettering is used to identify or designate each individual tube that is produced. This is an important processing step, since it guarantees that each tube that is used to make a product can be traced back to its manufacturer.
- Trimming – This processing step is carried out on tube ends that need to be absolutely straight. If the tube does not have a straight end or if the straight end is too short, the tube is bent at its ends with an offset before being successively trimmed.
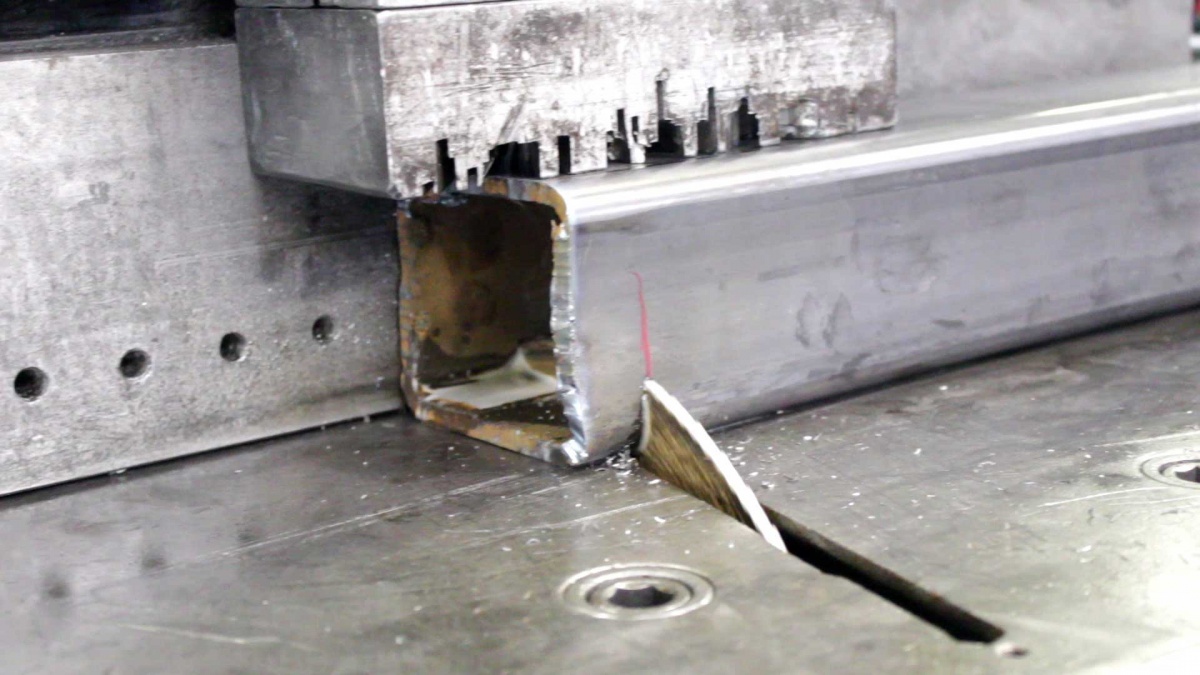
- Thread cutting – A processing step used to drill a threaded hole in the tube so that a bolt can be inserted into the tube. In this case, the drilled hole must be perfectly round (not oval) to ensure the bolt can be screwed in easily.
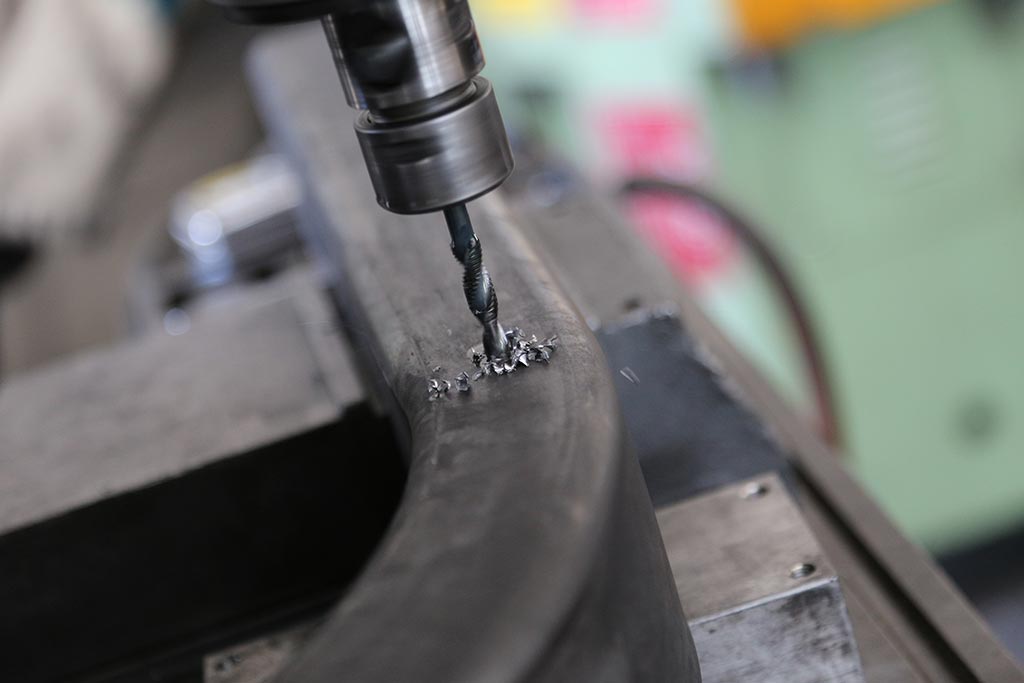