Bending or rolling or roll bending aluminium tubes (aluminium pipe bending) and aluminium sections (aluminium profile bending) is achieved by cold forming or cold bending.
There are key differences between these two bending methods for aluminium tubing and sections.
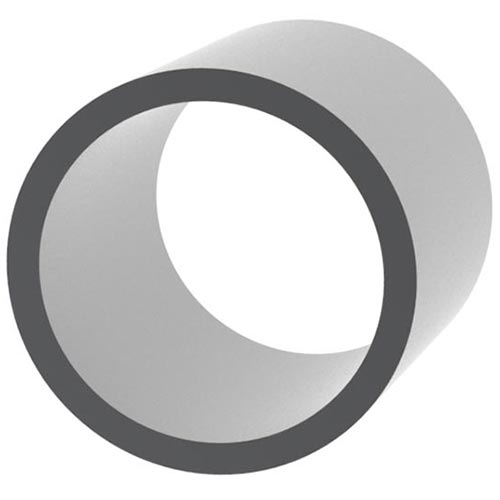
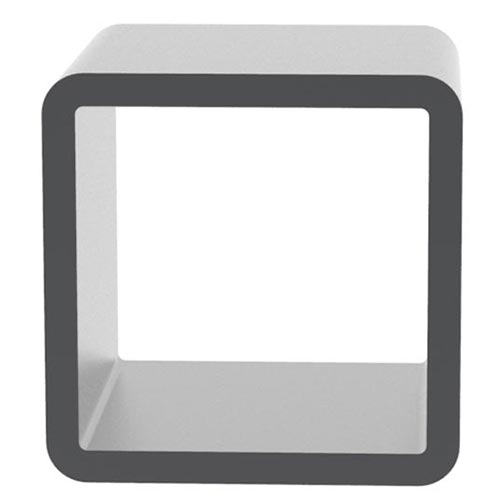
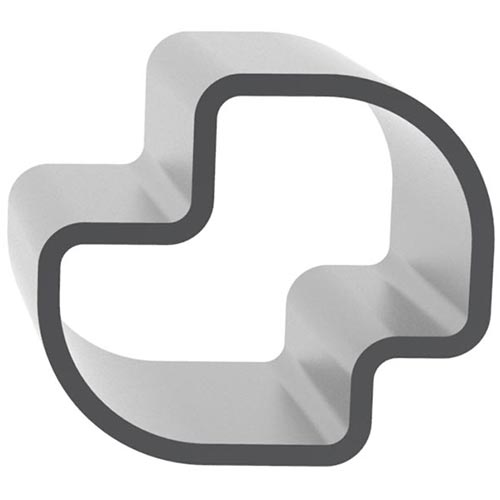
Using cold forming to bend aluminium tubes and sections
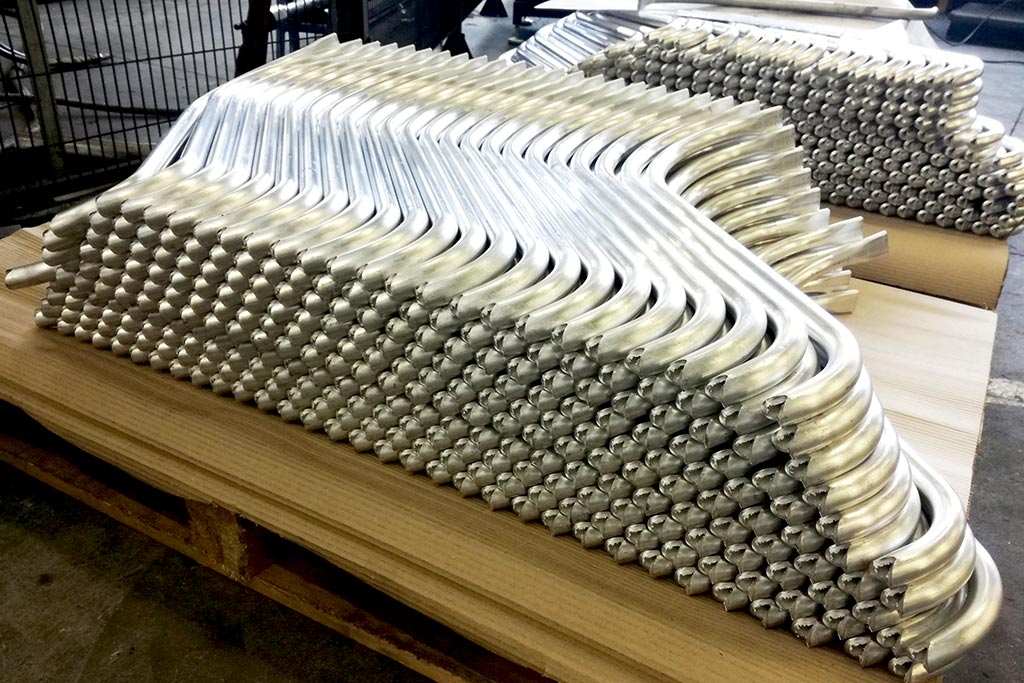
Bending aluminium tubes or sections is achieved using cold forming. This bending method is also called cold bending, since the process is completed at room temperature and without prior preparation of the material.
The tube is bent by being placed in special tube bending machines.[T1]
The bending of aluminium tubes and sections (bending aluminium extrusions) by cold forming is typically carried out by using CNC tube bending machines.
These machines guarantee maximum bending precision and a more efficient production process.
Bending aluminium sections
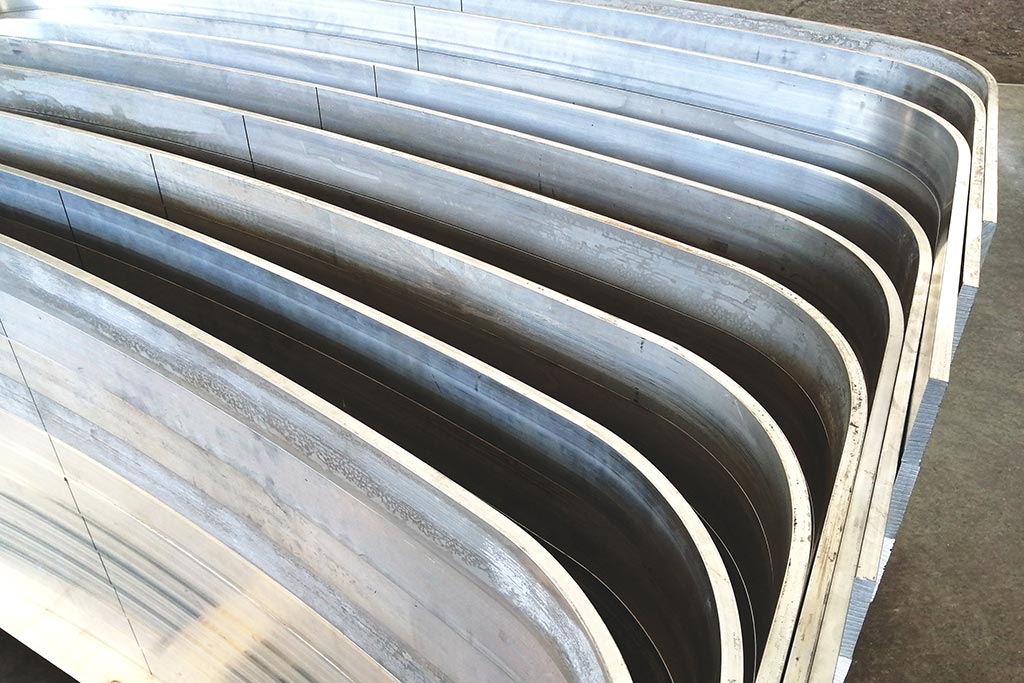
The other method for bending aluminium sections, also achieved with cold forming, is referred to as tube rolling or roll bending.
This method allows much larger bending radiuses to be achieved than with conventional bending. Roll bending aluminium tubes and sections also offers other advantages:
- More than one bending radius can be achieved on a single tube section
- Sections with different radiuses can be obtained
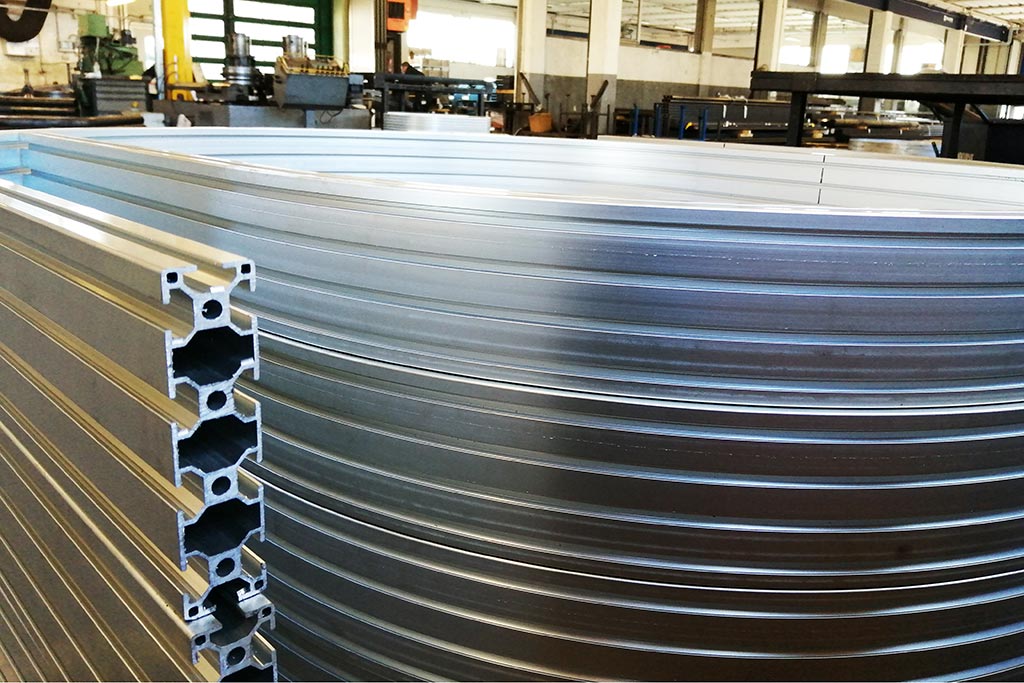
Industrial applications for bent aluminium tubes
Alongside steel and stainless steel, aluminium is one of the commonest alloys encountered in the world of cold forming and aluminium tubes are used in a wide range of industrial applications. Key reasons why bent aluminium tubes and sections are a preferred choice include:
- Softness
- Light weight
- Resistance to oxidation
- Visual appeal
One key characteristic of aluminium tubing is its capability to dissipate heat – which is better even than that of copper tubing.
Due to their tolerance of very high temperatures, aluminium sections are frequently used in the construction of LED lighting systems.
Thanks to their many positive qualities, aluminium tubes are also used for the construction of products where low weight and visual appeal are especially important, including:
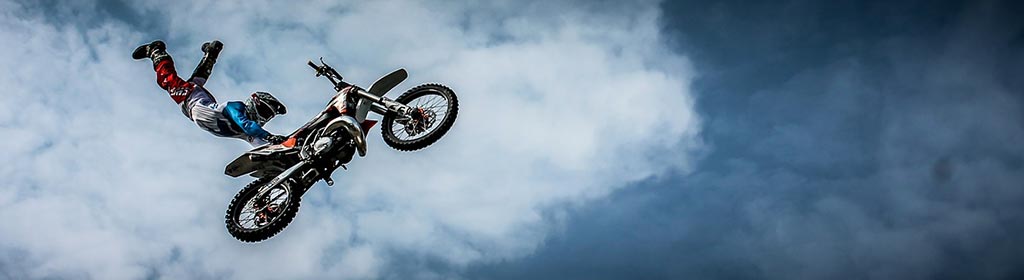
Before a specific bending method is used to create aluminium bends during the manufacture of one of the products mentioned above, an analysis always needs to be completed to determine the feasibility of the tube bending process.
Products made from bent aluminium tubes are used in many industry sectors. Examples include:
- Transport
- Building
- Machinery construction
- Furniture
- Automotive
- Shipping
Properties of aluminium tubes and sections
Aluminium is a ductile, silvery metal that is usually harvested from bauxite ore.
The silvery colour of the aluminium tube can be attributed to the oxide layer that forms on the surface when it comes into contact with air. This works to prevent oxygen coming into contact with the aluminium underneath the oxide layer, giving it excellent protection against corrosion.
The aluminium that is used in the manufacture of tubes and sections, which are then bent using tube bending or roll bending, is referred to as a metal alloy, since it is obtained by melting various metal(loid)s together in varying proportions for casting:
- Aluminium
- Copper
- Zinc
- Manganese
- Silicon
- Magnesium
The actual melting point of aluminium depends on the respective composition of the alloy from which the aluminium tube was manufactured. The melting point of pure aluminium is 660 °C. The various aluminium alloys determine several important properties, including:
- Mechanical strength
- Ductility
- Corrosion resistance
As we will see shortly, the alloy used for the aluminium section is not of merely theoretical interest: the choice of aluminium alloy directly influences its capabilities for processing while also determining the range of applications and usage scenarios for the finished aluminium tube or section.
If the alloying element used in an aluminium alloy is copper, for example, then the aluminium section will have good mechanical strength and weldability but less resistance to corrosion than aluminium alloys whose alloying elements are magnesium or silicon.
Apart from round tubes, square tubes and aluminium sections can also be bent. The choice of tube shape – whether bent, round, square or rectangular – is often made for reasons of aesthetics or design.
Properties of bent aluminium tubes and sections
When choosing an aluminium tube or bent aluminium section instead of some other alloy, such as a steel tube, for example, many qualities can be important for the final decision:
- Elongation
- Yield point
- Tensile strength
- Hardness
- Toughness
- Ductility
- Hardening capabilities
- Visual appeal
- Weight
Steel and bent stainless steel tubes are mainly used for the construction of products and machinery where a high degree of breaking strength and load strength is required – such as for agricultural machinery.
In contrast, aluminium sections and tubes are utilised if a lightweight part with high visual appeal is important – e.g. for bicycle frames.
Bending and processing aluminium tubes
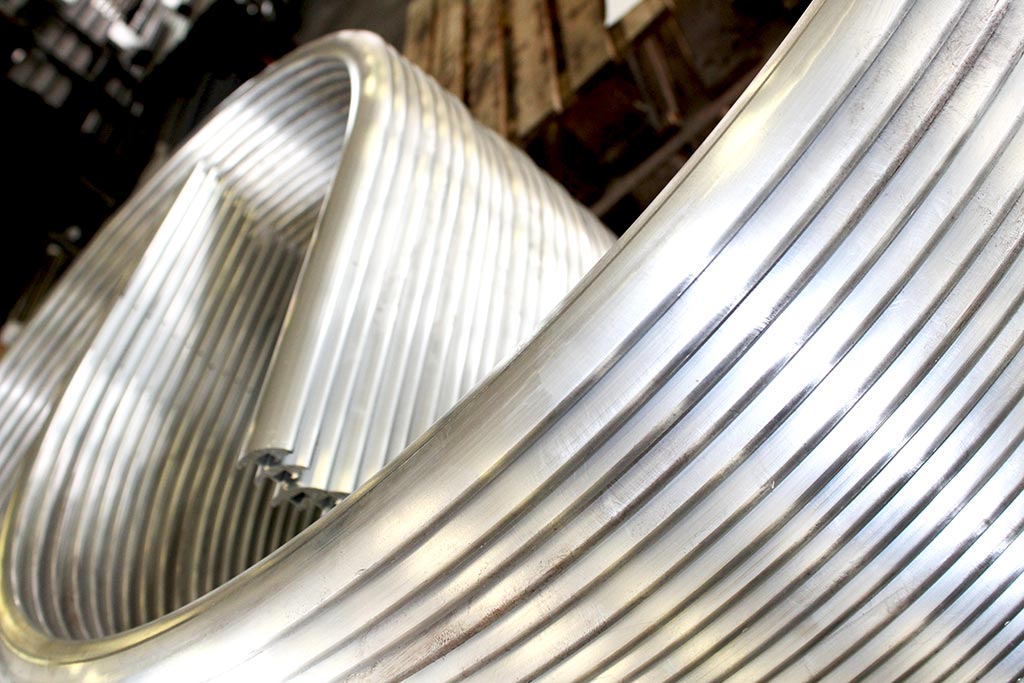
The processing of aluminium tubes and sections is not limited only to bending and roll bending. However, a distinction needs to be made between two kinds of aluminium tube processing:
- Processing before tube bending
- Processing after tube bending
As one example, the laser cutting of tubes can only be carried out before bending the tube – and not too near the zone of deformation.
The most important kinds of tube processing carried out with a tube laser – and before bending the tube – include:
- Drilling
- Countersunk holes
- Buttonholes
- Angled tube cuts
- Marking
Typical kinds of tube processing carried out on aluminium sections that are already bent include:
- Thread cutting
- Trimming
- Milling
- Pressing
Aluminium alloys
The specific aluminium alloy used determines a number of key properties for aluminium sections and tubes. The alloy type affects the machinability of aluminium sections, including their capabilities for bending and folding. The aluminium alloy is especially important for the following qualities:
- Mechanical strength of the tube
- Corrosion resistance
- Electrical conductivity
- Thermal conductivity
The following table presents the 9 aluminium alloys from which rolled and bent aluminium tubes and sections are made, and the most important industry sectors in which they are used:
1000 SERIES
MAIN ELEMENT(S)
–
This is not actually an alloy as such but instead aluminium itself in different grades of purity.
Low mechanical strength, high resistance to corrosion, high thermal and electrical conductivity.
TYPICAL APPLICATIONS
Sections for heat exchangers, electric condensers, packaging, signage, food industry
2000 SERIES
MAIN ELEMENT(S)
COPPER (Al-Cu)
Aluminium tubes made from this alloy have low corrosion resistance but a higher mechanical strength.
TYPICAL APPLICATIONS
Bent sections for military aviation, plastic injection moulding, high-precision tools
3000 SERIES
MAIN ELEMENT(S)
MANGANESE (Al-Mn)
Series 3000 aluminium tubes have high mechanical strength, low ductility and good resistance to corrosion.
TYPICAL APPLICATIONS
Aluminium tubes that are used for making household appliances and transportation machinery
4000 SERIES
MAIN ELEMENT(S)
SILICON (Al-Si)
These aluminium sections have low thermal expansion but are very hard-wearing.
TYPICAL APPLICATIONS
Welding
5000 SERIES
MAIN ELEMENT(S)
MAGNESIUM (Al-Mg)
Aluminium tubes made from this alloy have high ductility and are suitable for a wide range of processes. Tubes exhibit high resistance to corrosion and good weldability.
TYPICAL APPLICATIONS
Parts for boats, ships, vehicle bodies
6000 SERIES
MAIN ELEMENT(S)
MAGNESIUM AND SILICON
(Al-Mg-Si)
Tubes made from this aluminium alloy are subjected to a special heat treatment process and have average mechanical properties. The tubes have good corrosion resistance and weldability.
This series includes the aluminium alloy 6060, which is the best kind of alloy for aluminium tube bending!
TYPICAL APPLICATIONS
Furniture, shipbuilding, frames, street furniture, equipment for trains, buses and subway trains, bent aluminium sections for making light fixtures. Tubes are also used in the automotive sector. Discover more about precision aluminium pipe bending
7000 SERIES
MAIN ELEMENT(S)
ZINC (Zn)
The presence of zinc in this alloy, which is produced with heat treatment, increases its strength and hardness, and means the alloy also develops better mechanical properties than other aluminium alloys.
TYPICAL APPLICATIONS
Bent aluminium tubes that are used in the production of motorbike and bicycle frames or other means of transportation
8000 SERIES
MAIN ELEMENT(S)
MIXED ALLOY
These tubes have a lower density but a higher mechanical strength. Aluminium tubes made from mixed alloys retain their toughness even at low temperatures.
TYPICAL APPLICATIONS
Bent tubes made from this aluminium alloy are mainly used in aerospace applications.
9000 SERIES
MAIN ELEMENT(S)
–
Series for experimental alloys.
TYPICAL APPLICATIONS
–
Treatment and finishing of bent aluminium tubes
Certain kinds of aluminium tube processing – such as special treatments and types of finishing – can only be carried out after bending is complete.
The reason for this is that the equipment used to bend the tubes can create imperfections in the tubes that would affect both visual appeal and the intended purpose of the tube.
The most important types of processing for bent aluminium tubes are as follows:
- Polishing – (also referred to as ‘brushing’) is a mechanical cleaning process that can be carried out with abrasive papers or special kinds of brushes.
- Anodisation – anodised aluminium has better resistance to scratching caused by wear and tear.
- Barrel finishing – a cleaning process for aluminium that removes metal residues created by earlier steps in processing.
Aluminium tube bending: information about cold forming
Bent sections and tubes made from aluminium are used in a wide range of industrial applications. Unlike other alloys such as steel, for example, all bending here is carried out as a cold forming process.
Bent aluminium tubes are typically used on account of their light weight and their visual appeal.
Accordingly, car and motorbike chassis as well as bicycles are often made from aluminium or the more expensive titanium.
Often, however, bending or roll bending is not the only processing step that bent aluminium tubes pass through before they are finished. Industrial use of aluminium tubes requires other kinds of tube processing, which include welding, laser cutting and anodisation, to give the finished aluminium tube a certain set of properties.
In all cases, the right aluminium alloy needs to be chosen to match the intended use.
Looking to bend your aluminium tubes? Then you have come to the right place. Send us your enquiry today!