Difference between bending and roll-bending metal tubes
The origins
The actions of bending and roll-bending metal tubes are technically known as cold plastic deformation processes (CPD), and they are generally understood to go back about 100 years, to the 20th century.
Bent and roll-bent steel tubes were used in sectors such as building construction, agriculture and interior design. These techniques made it possible to use tubes in ways that had been impossible until then.
Just think, for example, of the frames required by agricultural machinery, of trailers for forestry machines, of the many uses in light and heavy carpentry. It is only thanks to the development of bending and roll-bending techniques that steel tubes have found such widespread use in modern industrial production.
This led to the founding of the first companies engaged in the production of machinery for bending and roll-bending tubes, i.e. CPD equipment. Initially, the processes possible with these machines were limited to round steel tubes, while modern machines can also process square and rectangular tubes and section bars.
Although these machines have existed for almost a century at this point, the market did not begin to express a strong demand for steel tubes for “new uses” requiring these processes until the late Seventies.
In response to the growing market demand, more companies began to specialize in producing CDP equipment, and one of these was Tecnocurve. After more than 25 years in business, we have become a highly specialized supplier, widely respected for our reliability, with customers in every part of the world.
Bending metal tubes: what does it consist of?
Bending effectively means deforming a tube or section bar with a relatively narrow radius of curvature that in relation to the diameter of the tube may vary from a minimum of 1.5 times the tube Ø, up to a maximum of 5 times. Metal tubes are bent with special machines called tube benders. The metal tube is given the shape of the bending die previously installed on the tube bending machine.
The most difficult aspect in bending metal tubes is limiting the deformation.
Inevitably, there will be some deformation of any metal tube when it is bent mechanically.
This deformation alters the tube only in the area in which it is bent, particularly in the inner and outer portions of the bend, as can be seen in the illustration below.
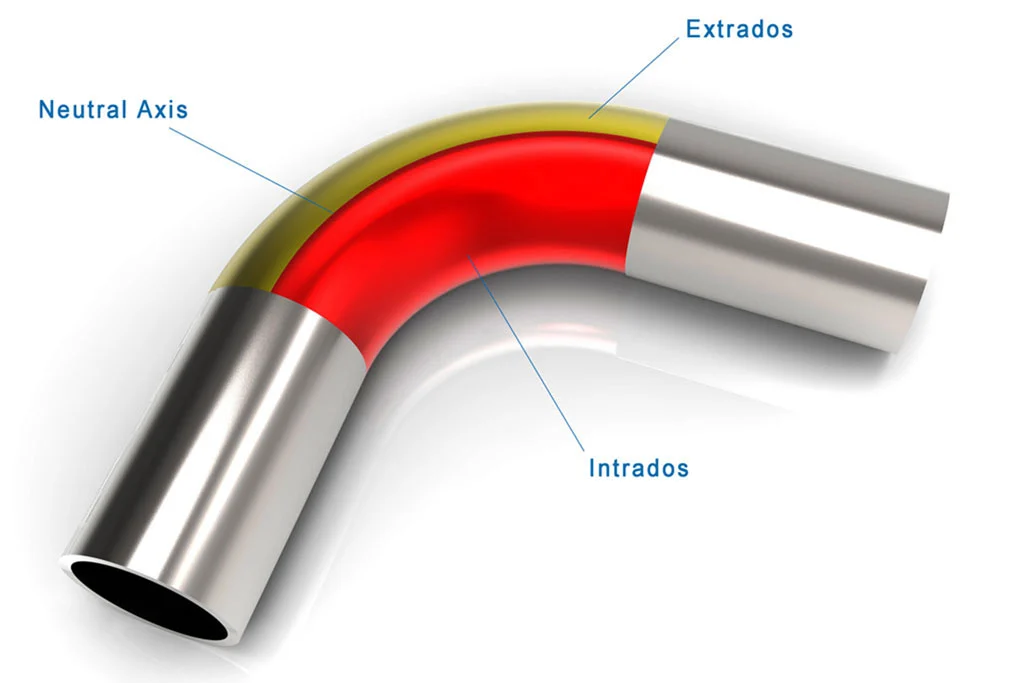
The intrados, shown in red, is the inner portion of the bend and is subject to compression stresses due to the difference of linear development between the average radius and the inner radius. In the most critical cases, this will cause “crumpling” of the material, shown by the more or less obvious creases in the steel tube.
The yellow part, called extrados, is subject to traction or elongation stress, which results in a thinning of the steel tube caused by bending.
The neutral axis, on the other hand, is a state of absence of stresses, which is not found, as we might expect, in the median portion of the tube but, balancing the tensional status of the piece, usually tends to move into the inner portion of the bend, toward the intrados.
The factors to bear in mind to improve the quality of the bend in a steel tube are:
- The ratio between the average radius of curvature and the diameter/thickness of the tube
- Elongation of the material
- Elastic return
- Esthetics
Bending
To bend tubes, whether of steel or of aluminum, special tube bending machines are used. The operation of these machines is mainly electromechanical. Thanks to technological progress, modern tube bending machines use FULL ELECTRIC technology, which makes it possible to speed up production and improve repeatability of the bent parts, while at the same time guaranteeing minimum margins of error, even on very high production runs.
What types of steel tubes can we bend?
Tecnocurve has 10 tube benders in its fleet, three of which incorporate the latest FULL ELECTRIC technology and can bend the following types of material:
- Round tubes from Ø 4 to Ø219
- Square/rectangular tubes with sections that go from 10×10 mm up to 120×120 (even 150×100)
- Various section bars
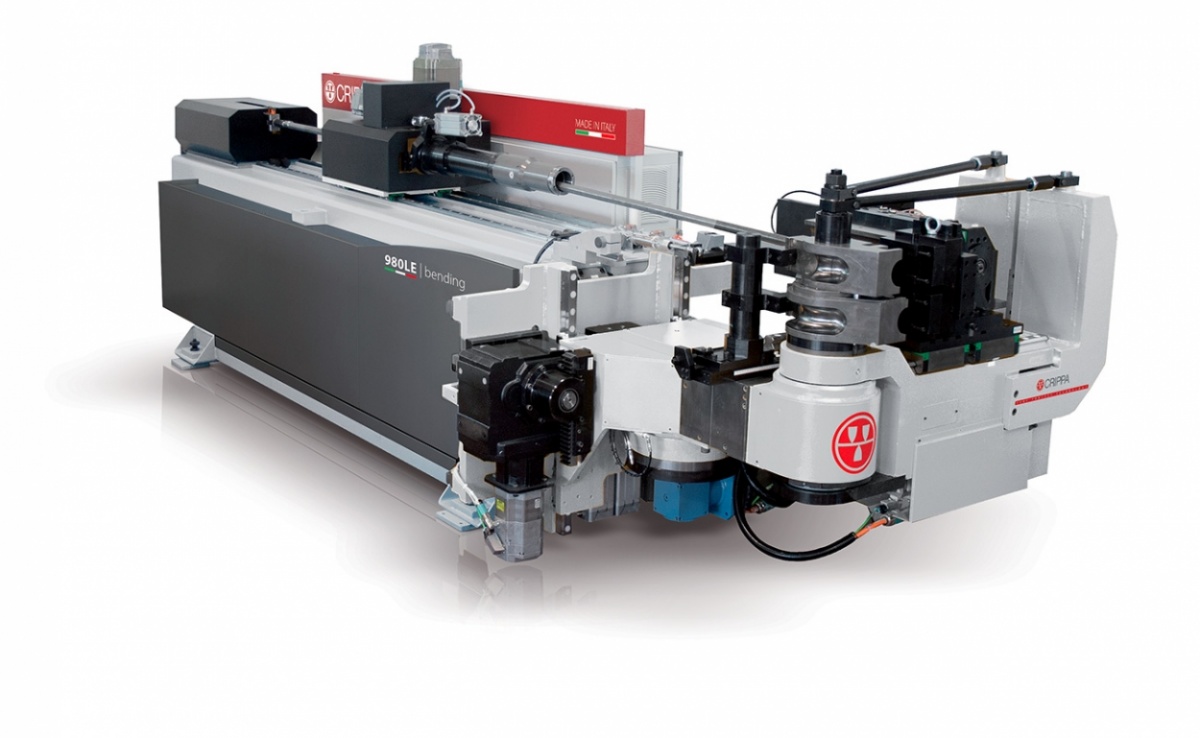
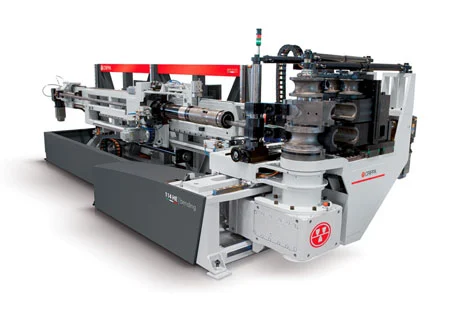
Equipment necessary for tube bending
Tooling a tube bender, whether its operation is mechanical or CNC, requires common parts, usually consisting of the following elements:
- Bending die
- Flange (only for square and rectangular tubes)
- Clamp
- Counter-clamp
- Fixed or hinged mandrel (depending on the difficulty of the bend)
- Slide
- Counter-slide (only for particularly difficult bends)
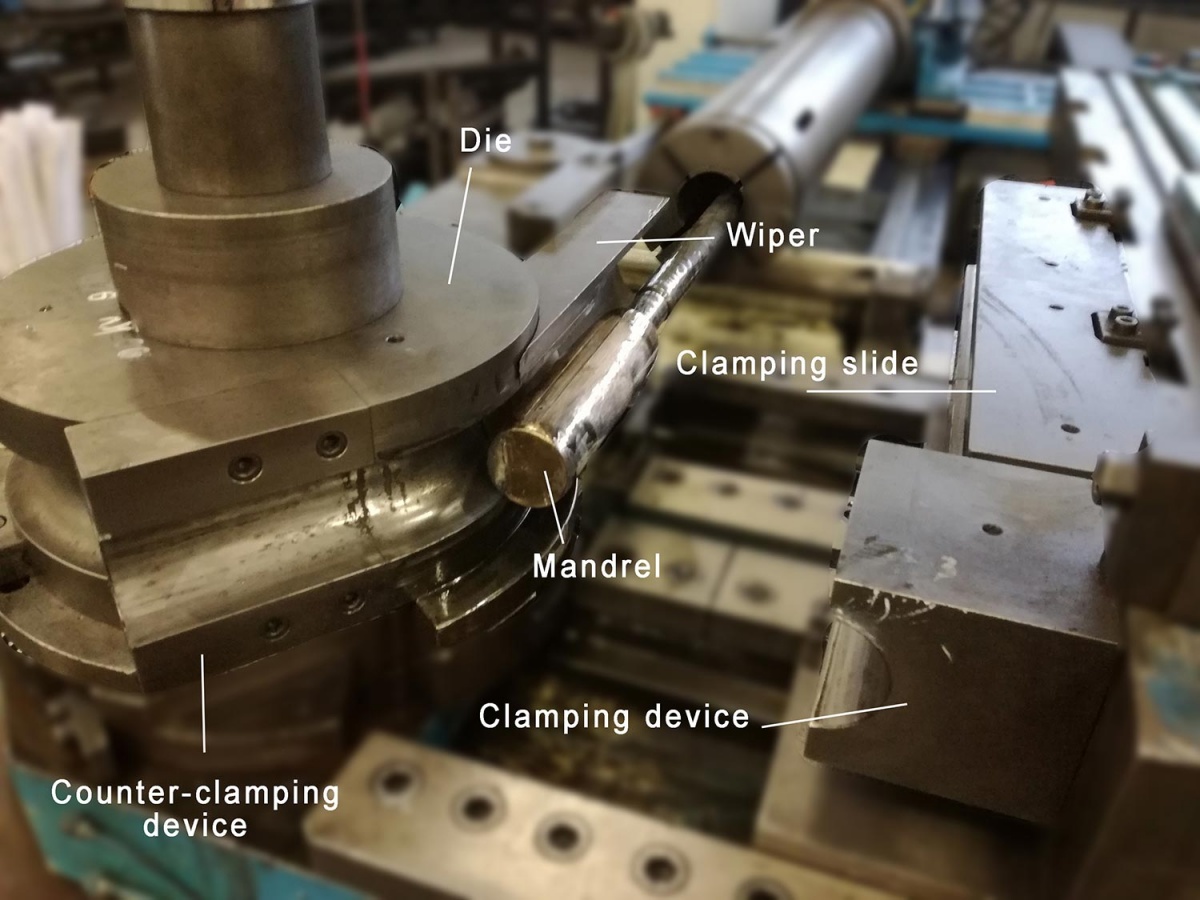
Roll-bending of tubes: what does it consist of?
Roll-bending is a process whereby we obtain cold process deformation with a wider bend radius that theoretically can range from 5 times the cross-section to infinity. To achieve this process, the equipment used consists of roll-bending machines.
The steel tube is made to pass through a set of three rollers that, after one or more passages (depending on the difficulty of bending), will form an arch with the required radius of curvature. Roll-bending is, generally speaking, a simpler process than bending.
The particular feature of this type of mechanical process is that a single machine can produce different bend radii on the same tube, permitting the creation of complex geometrical shapes.
The disadvantage of roll-bending is the fact that in order to achieve a valid grip and begin the roll-bending process, the machine requires a portion of additional material at the beginning and end of the tube. This necessitates an increase in the total quantity of metal needed to roll-bend the tube.
Roll-bending machine
The roll-bending machine is characterized by the presence of three shafts, each of which is fitted with a roller having the contours of the tube, tubular element or section bar to be bent.
Its function is hydraulic, but modern digital roll-benders are equipped with a screen where the operator can read data and measurements. It is also possible to perform processes on tubes in manual or automatic mode. The speed of the shafts is adjustable, as is the distance between the rollers.
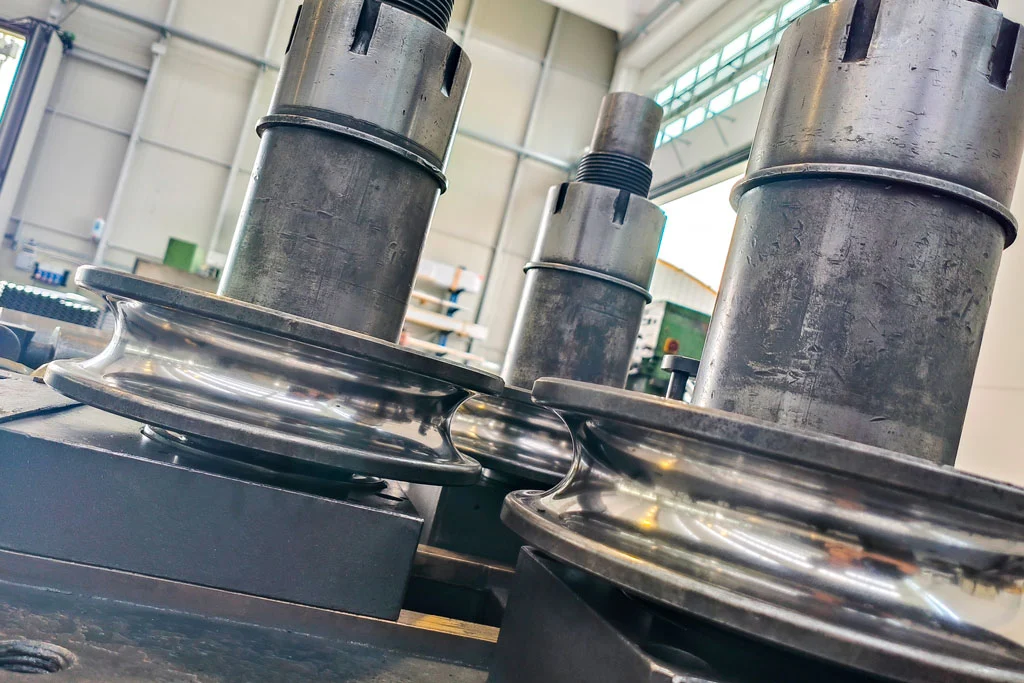
What types of steel tubes are suitable for roll-bending?
- Round tubes from Ø11 mm to Ø154 mm
- Square/rectangular tubes with cross-section from a minimum of 6×6 mm up to 150×100 mm
- Various section bars
Equipment necessary for roll-bending tubes
Roll-bending is a simpler process than bending, and does not require the use of much equipment. All that is necessary are three specially contoured rollers for each section of steel tube or section bar, through which the material is passed to give it the desired cold process deformation.
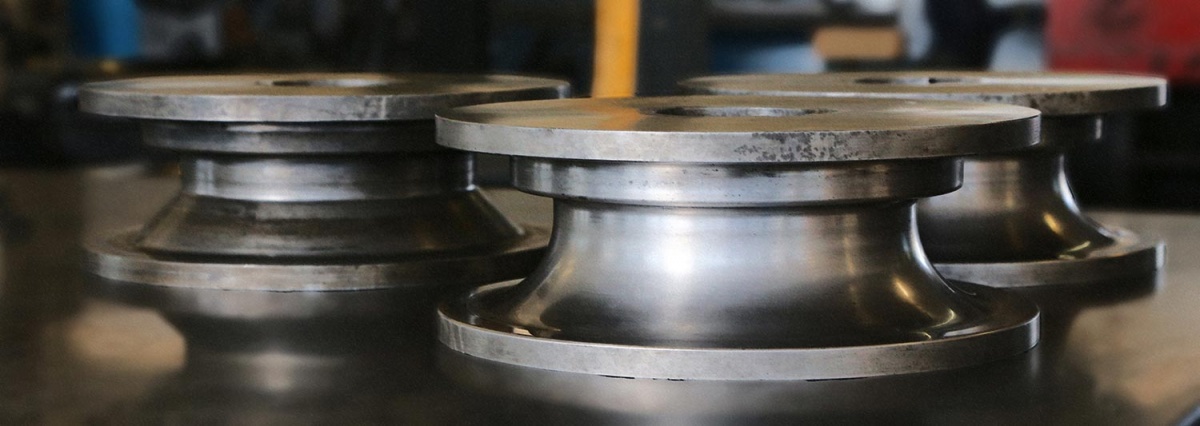
- Special rollers are prepared that follow the contour of the bar (generally for complex section bars in aluminum).
- Nylon blocks are produced to match with the bar for roll-bending, so as to simulate a closed structure like a tubular element.
What materials can be bent and roll-bent?
- Steel tubes
- Stainless steel tubes
- Aluminum tubes
- Tubes in titanium – particularly for the automobile sector.
- Brass tubes – in thin plates or solid blocks, usually used in the lighting sector.
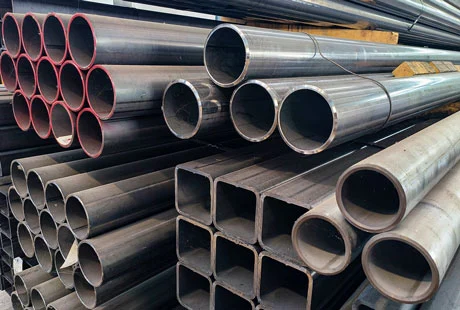
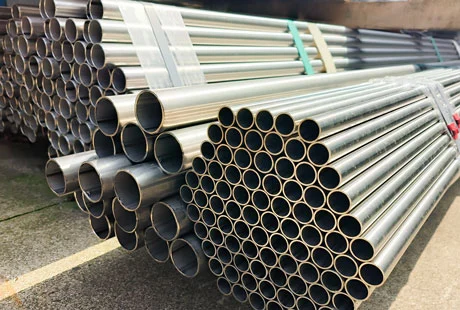
To bend or roll-bend?
As we have seen above, the main difference between bending and roll-bending is the radius of curvature – narrow or wide – of the tube. The second difference is that roll-bending is the only technique that can be used to bend the same metal tube with different bend ratios. In this sense, we also speak of variable bend radius.
To have a more precise idea of what the minimum bend radius is, we have to multiply the tube diameter by five. If, for example, the tube diameter is Ø50 mm., the minimum roll-bending radius is 250 mm. To obtain a smaller bend radius it will be necessary to bend the tube with a CNC tube bender.
The minimum bend radius is calculated with a special formula that gives us a coefficient; if the coefficient exceeds a certain value it determines the feasibility of bending for a specific radius.
In bending steel, the use of special equipment contributes to the quality of the bent tube, above all in those cases in which the aforementioned coefficient is at the limit of feasibility.
It is possible to bend and roll-bend the same tube?
While in the past, however, the parts of the metal tube were bent and roll-bent separately, then welded, today the processes are done in a single procedure, without recourse to welding the tube. This simplifies the production process and prevents the risk of cracking in the area around the joints.
This type of combination can be managed by performing the bending operation on one machine and the roll-bending operation on another, or it can be done on a single CNC tube bending machine. With the modern CNC tube bending machinery it is possible to install both bending and roll-bending equipment. In this way, it is possible to obtain complex geometrical shapes in less time than it would take to prepare two machines.
Tecnocurve has a vast number of tools for bending and roll-bending, and can produce almost all the tube bend radii required for different industrial applications. Where the dies are not available, it can produce the necessary tooling internally. To do this, Tecnocurve disposes of a lathe with numerical control mod. LA-250ML made by Talisawa and two CNC V8 work centers by Akira.